Linearized Joint Interface
A linearized joint interface that delivers greater predictability and reduced variation in the structural response of complex assemblies
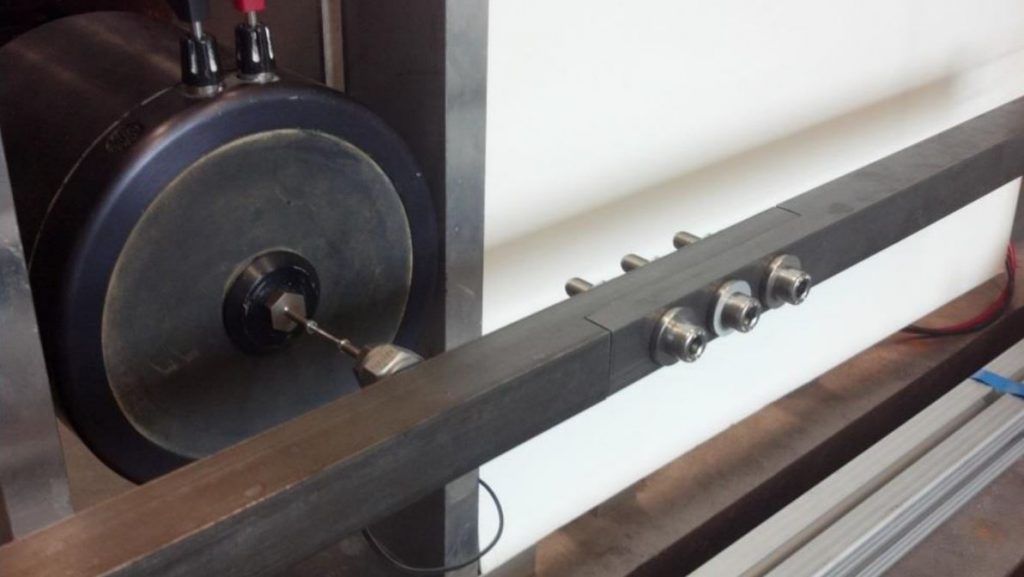
Predicting the dynamic properties of a structural system is particularly valuable for manufacturers of large assemblies because structural dynamics are notoriously difficult and complex to model. Even with intensive testing, order-of magnitude variability and costly failures persist in final assembly. Researchers at Sandia National Laboratories have developed a linearized joint interface that minimizes the relative motion between two interfaces, thereby offering greater predictability and reduced variation within structural systems. This development reduces structural uncertainty with a simple-to-fabricate design that decreases costs associated with modeling, testing, and waste, particularly for manufacturers of large or complex assemblies. In this approach, a joint interface’s structural dynamic properties are made independent of response amplitude with a redesigned interface geometry. To achieve this, the interface geometry includes two approaches for limiting contact in key areas, which can be applied to lap joints with an arbitrary number of bolts as well as a range of other joint types.
Benefits
- Greater predictability compared to conventional joint interfaces
- Reduced variation in mechanical assemblies
- Improved repeatability in manufacturing and assembly environments
- Enhanced damping capacity
- Simple fabrication
Applications and Industries
- Aerospace
- Assembly
- Automotive
- Manufacturing
SD#14184
Published12/20/2019
Last Updated12/20/2019